Валы и корпусные детали в различных машинах и механизмах часто получают незначительные повреждения, которые необходимо измерить и восстановить. Задача осложняется из‑за имеющихся в деталях углублений, пазов и глухих отверстий, недоступных для микрометра или других специальных измерительных инструментов.
С такой проблемой метрологи и инженеры сталкиваются постоянно, но не все знают, что эффективно решить ее можно с помощью технологии 3D‑сканирования.
Преимущества 3D‑сканеров
3D‑сканеры становятся неотъемлемой частью производственных процессов при решении задач контроля качества и обратного проектирования, особенно в диагностике, ремонте и профилактическом ТОиР, в импортозамещении комплектующих и усовершенствовании конструкторских решений.
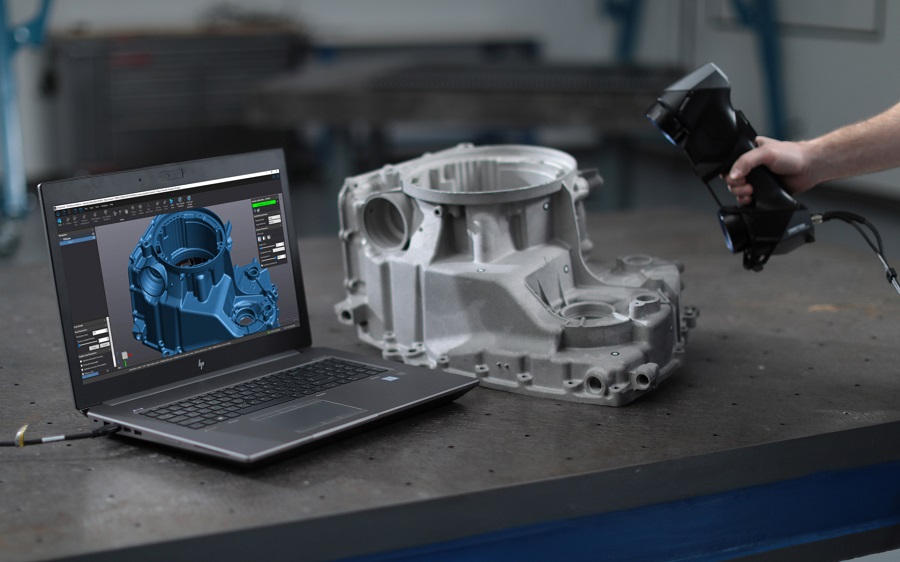
Устройства 3D‑сканирования обеспечивают высокую точность, гибкость и быстроту измерений сложных объектов, могут работать автономно, просты в эксплуатации, по всем параметрам превосходя традиционные ручные инструменты. Возможность получения точных 3D‑данных о труднодоступных участках деталей, узлов и оборудования для последующей диагностики – одно из несомненных преимуществ ручных лазерных сканеров.
3D‑диагностика и восстановительный ремонт оборудования
Процесс восстановления посадочных мест с использованием этой технологии включает в себя несколько ключевых этапов.
- Диагностика глухих и труднодоступных корпусных отверстий и валов с применением отработанной методики 3D‑сканирования.
- Подготовка изделия к наращиванию восстанавливающего слоя нужных параметров и состава.
- Нанесение металла на изношенное посадочное место. Толщина наносимого слоя может варьироваться от 5‑7 мкм до 2 мм, что позволяет достичь оптимального результата.
- Расточка или шлифовка детали. При необходимости деталь может быть подвергнута механической обработке для получения требуемого размера.
- Проверка изделия по геометрическим параметрам с помощью 3D‑сканера и специализированного ПО для контроля качества.
Рассмотрим, как решаются две типичные проблемы – неравномерный износ вала по диаметру и просадка корпусных отверстий.
Проблема 1: неравномерный износ вала по диаметру
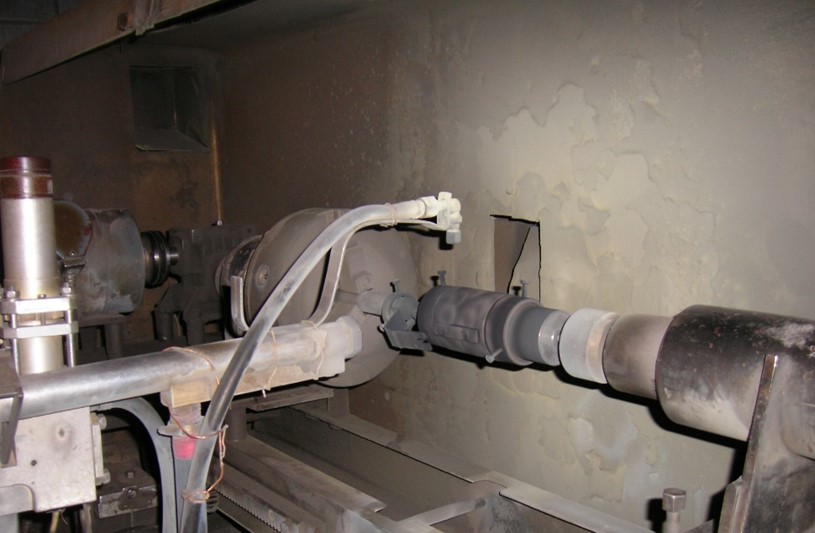
Частный пример представлен на рис. 2. Нанесение восстанавливающих и специальных защитных покрытий на валы распространено и в производстве, и в восстановительных процессах, в том числе в насосной и компрессорной промышленности, в ремонте автомобильной техники при отсутствии запчастей.
Сначала необходимо выполнить 3D-сканирование, которое позволяет оценить степень износа по цифровой модели вала.
На основании этой оценки назначается толщина восстановительного покрытия. Мы видим, равномерно или неравномерно надо наносить покрытие, где нужно усилить нанесение и предварительно назначить стратегию восстановления детали. Затем контролируется нанесение покрытия.
В процессе нанесения покрытия на поверхности образуется волнистость. На глаз и даже измерительным инструментом иногда не представляется возможным определить, попали ли мы в размер на всей поверхности, особенно если она достаточно обширная и где‑то есть провалы в геометрии. При мехобработке обнаружится, что поверхность имеет структурные дефекты. 3D‑сканирование позволяет оценить размер нанесенного слоя без необходимости снимать деталь.
Проблема 2: просадка корпусных отверстий
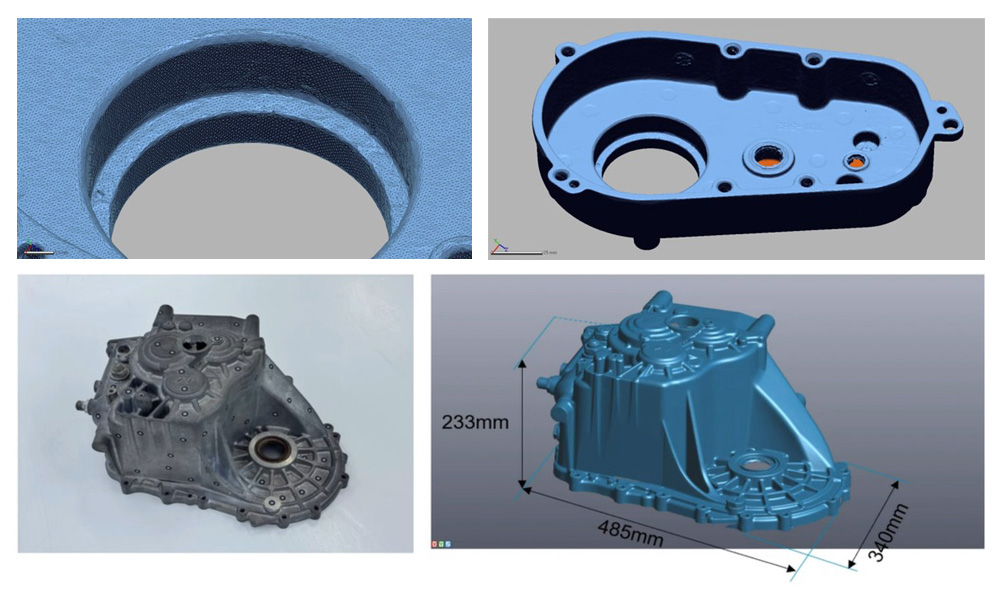
Еще один эффективный способ – сканирование отверстий в корпусных деталях. С помощью 3D‑сканера можно с точностью до 15 микрон оперативно оценить состояние и степень просадки отверстий и посадочных мест под подшипники. Особую ценность данная методика представляет для глухих отверстий в сложных корпусных деталях типа крышек редукторов.
На основе полученных данных выбираем оптимальную стратегию восстановления:
- Если просадка небольшая, без механической обработки можно нанести пару десятков микрон на сторону и восстановить посадку под подшипник.
- Если же просадка существенно больше, то следует изменить стратегию обработки: нанести больший припуск под мехообработку и потом обработать поверхность, оценивая с помощью 3D‑сканирования технологический процесс и достаточность нанесения покрытия.
3D‑сканирование покрытий при производстве или для восстановительных работ
В процессе нанесения покрытий методом газотермического напыления важно контролировать толщину и рельеф наносимого слоя. Технология 3D‑сканирования применительно к этой задаче позволяет сравнить базовую модель и отсканированный объект в специализированном программном обеспечении.
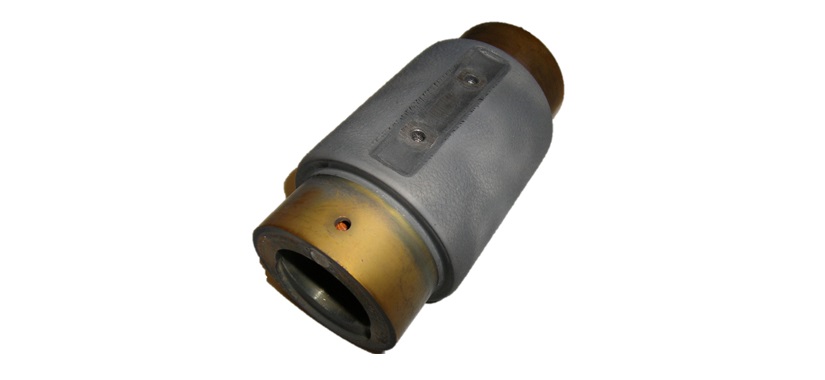
Преимущества
- Не требуется демонтаж детали: сканирование можно проводить прямо на приспособлении или оснастке.
- Контроль толщины покрытия: можно легко убедиться, что толщина покрытия достаточна для заданного размера, а также учесть припуск на механическую обработку. В результате экономится время – весь процесс занимает несколько минут.
- Высокая точность контроля: сканирование выполняется с точностью до 15 микрон.
- Универсальность: сканирование может применяться для поверхностей любых форм и размеров, технология в первую очередь актуальна для длинных валов и больших площадей.
Реальный технологический процесс был отработан и показал свою эффективность. На рис. 4 мы видим вал редуктора с покрытием в процессе восстановления. На валу была применена стратегия газотермического напыления с помощью детонационного напыления, и контроль производился в процессе нанесения покрытия с использованием 3D‑сканера.
Примеры восстановленных деталей
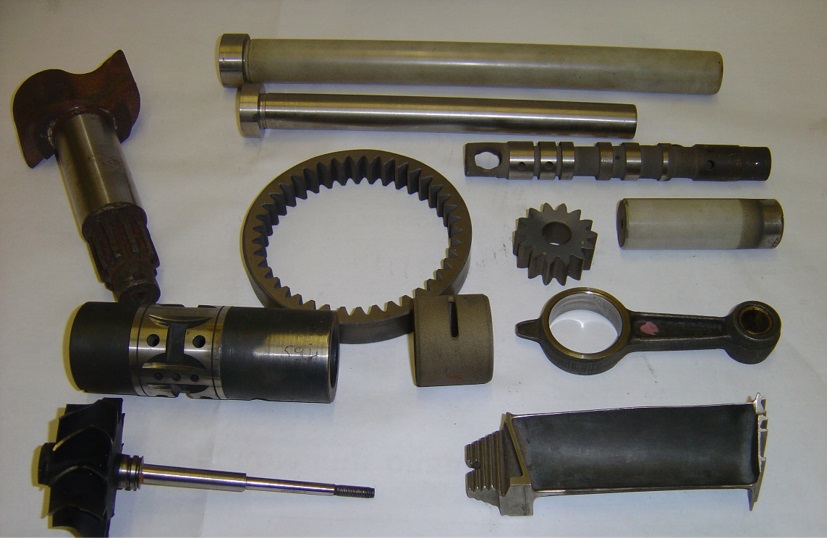
3D‑сканирование можно применять для оцифровки поверхностей любых форм и размеров. На рис. 5 представлено больше примеров изделий, на которые можно нанести восстановительное покрытие с применением сканера.
К ним относятся:
- валы со сложной геометрией и отверстиями
- насосные детали
- плунжеры
- крыльчатки
- лопаточные машины
- детали с различными пазами
- корпусные детали
Моделирование/сборка стыковочных узлов и деталей машин и механизмов
3D‑сканирование также предлагает решение на первый взгляд неочевидных задач – к примеру, моделирования и сборки стыковочных узлов и деталей сложных машин и механизмов. Речь идет об агрегатной сборке, последующей оценке полученной геометрии, сравнении с моделью и с чертежами.
Это особенно актуально:
- при сборке сочленений различных крупногабаритных узлов водного транспорта
- при оценке окончательной модели таких больших аппаратов, как дирижабли и экранопланы
Благодаря методике моделирования и монтажа стыковочных узлов можно обеспечить быстрый и эффективный процесс сборки и контроля таких сложных машин.
Услуги центра TWIZE
Сталкиваетесь с трудностями при выполнении вышеописанных задач? Поручите их команде центра экспертных 3D‑решений TWIZE.
Солидный опыт наших специалистов в реализации различных машиностроительных проектов позволяет не только грамотно выполнять сканирование и контроль геометрии узлов и механизмов, но и проводить анализ материалов и твердости поверхности, делать предварительные экспертизы и выводы о нанесенных покрытиях, их толщинах, физико-химическом составе, о различных сплавах и методах термической обработки, примененных на деталях. Таким образом, мы готовы выполнить углубленный анализ состава детали и технологии, по которой она была произведена.
Наша компания оказывает полный спектр 3D‑услуг, которые также включают обратное проектирование, разработку документации, предпроектные изыскания гражданских и промышленных объектов, а также промышленную 3D‑печать.